In a Nonwoven Spunmelt Machine, the calendering unit plays a crucial role in the production process, and the control of temperature, speed, and pressure is essential for achieving desired characteristics in the final nonwoven fabric. Let's break down how these parameters are controlled and their impact:
Temperature Control:
The calendering unit typically includes heated rollers or plates. The temperature is controlled through heating elements within these rollers. Precise temperature control is crucial as it influences the viscosity of the polymer and the bonding of the filaments in the nonwoven fabric.
Higher temperatures can enhance the bonding between the filaments, resulting in a denser and stronger fabric. However, excessively high temperatures can lead to polymer degradation and negatively impact the fabric's properties.
Speed Control:
The speed of the calendering unit refers to the rate at which the fabric moves through the rollers. Speed is controlled using motors and other mechanisms.
The speed affects the dwell time of the fabric between the rollers. A slower speed allows for more heat transfer and increased bonding, while higher speeds may lead to a lighter fabric with less bonding.
Pressure Control:
The pressure in the calendering unit is controlled by adjusting the gap between the rollers. Hydraulic or pneumatic systems are often used for pressure control.
Higher pressure can compress the fabric, improving bonding and reducing the thickness. However, excessive pressure may lead to over-compression and affect the fabric's breathability and softness.
Impact on the Final Nonwoven Fabric:
Fabric Density and Strength:
Higher temperatures and pressure contribute to increased bonding between filaments, resulting in a denser and stronger nonwoven fabric.
Thickness and Porosity:
Adjusting the speed and pressure affects the thickness of the fabric. Lower speeds and higher pressures typically lead to thinner fabrics, while higher speeds may result in a lighter and more porous structure.
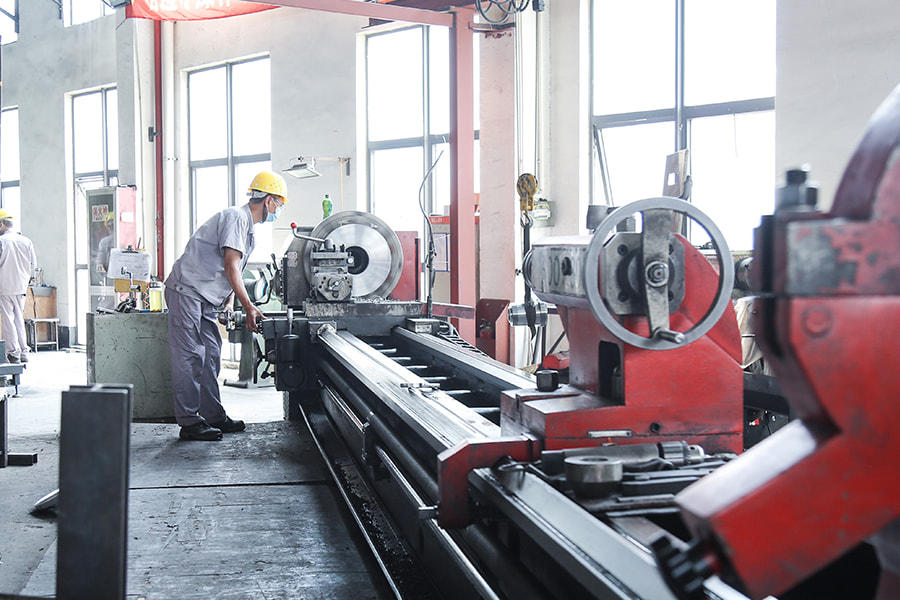
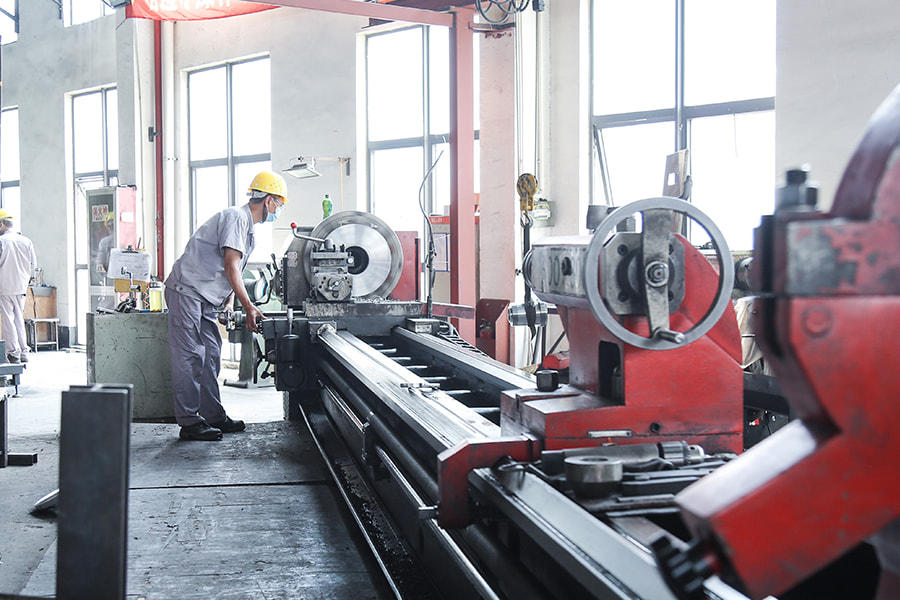
Surface Smoothness:
Control over temperature, speed, and pressure influences the surface smoothness of the fabric. Higher temperatures and pressures can create a smoother surface.
Breathability and Softness:
The interplay of these parameters impacts the breathability and softness of the fabric. Lower temperatures and pressures might result in a softer and more breathable fabric.
Uniformity:
Precise control of these parameters ensures uniformity across the fabric width, avoiding variations in properties.